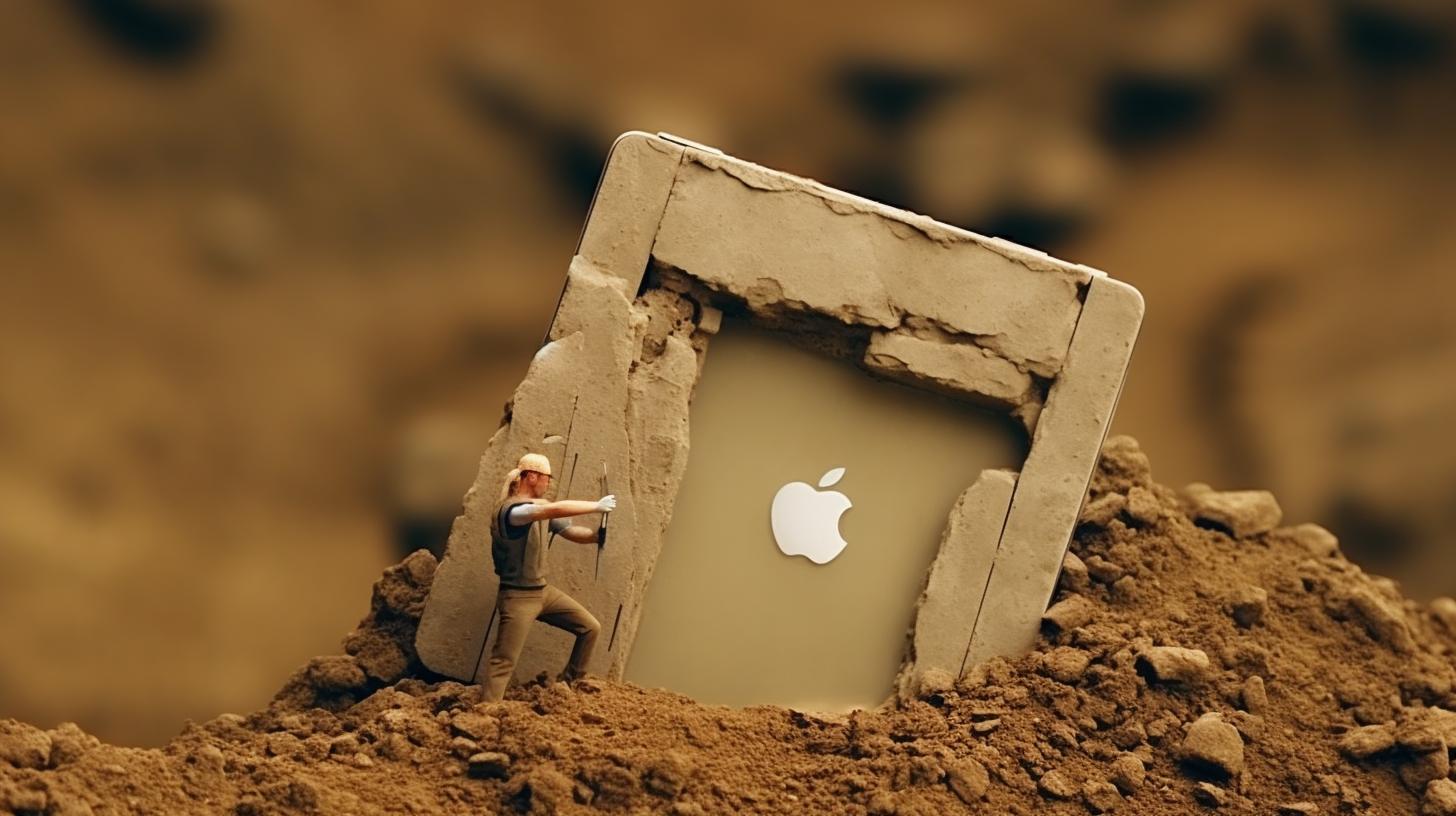
How is an iPad made? The process of transforming a concept into a tangible product involves various stages, from design and development to manufacturing and distribution.
This article provides an in-depth look at the evolution of the iPad, exploring its innovations in design and technology, the behind-the-scenes creation process, the manufacturing process from raw materials to finished product, quality control and testing, the role of automation and human labor in production, sustainability practices in manufacturing, and packaging, distribution, and marketing.
The iPad has come a long way since its conceptualization to becoming a reality. Innovations in design and technology have played a crucial role in shaping the components of every iPad. This section will delve into how these advancements have contributed to making the iPad what it is today.
One of the key aspects that will be explored is research and development (R&D) as well as product development. Getting a behind-the-scenes look at this stage will provide insight into how ideas are transformed into functional products through meticulous planning and testing. Understanding this process sheds light on the immense effort that goes into bringing every iPad model to consumers worldwide.
Innovations in Design and Technology
Material Selection and Design
The process of creating an iPad begins with careful material selection and design. Apple’s engineers work on selecting the most suitable materials for the different components of the iPad, considering factors such as durability, weight, and functionality. The design phase involves creating sleek and innovative designs that not only look visually appealing but also integrate seamlessly with the internal components.
Integration of Components
Once the materials are selected, the next step involves integrating various components such as the display, processor, memory, battery, and other electronic elements. This requires precise engineering and careful assembly to ensure that all the parts fit together perfectly. The goal is to create a seamless and efficient device that delivers exceptional performance.
Advanced Manufacturing Techniques
The manufacturing process of an iPad involves state-of-the-art techniques such as precision machining, injection molding, and advanced assembly methods. Each component is manufactured with precision to meet Apple’s strict quality standards. The utilization of advanced manufacturing technologies allows for high levels of precision and efficiency in producing each iPad.
As Apple continues to push the boundaries of design and technology in their products, the innovations in design and technology will play a crucial role in shaping the future of iPad production. The company’s commitment to excellence and continuous improvement drives them to find new ways to enhance the user experience while maintaining high-quality standards throughout every stage of production.
R&D and Product Development
The process of developing a new iPad begins with extensive research and development (R&D) to bring the concept to reality. This involves a team of engineers, designers, and product developers working together to create a prototype that meets the company’s standards for innovation and functionality. The goal is to push the boundaries of technology and design to deliver an exceptional user experience.
One key aspect of the R&D phase is determining how to integrate the latest technological innovations into the iPad. This includes exploring new components such as more powerful processors, higher resolution displays, advanced camera systems, and innovative input methods like Apple Pencil support. The team also fine-tunes existing features to enhance performance, battery life, and overall user satisfaction.
During product development, extensive testing is conducted to ensure that each component functions seamlessly with others and that the overall design meets rigorous quality standards. This involves rigorous testing under various conditions to simulate real-world usage scenarios. This phase also involves refining software integration and compatibility with third-party apps and accessories.
Next comes the pilot manufacturing stage where a small batch of iPads is produced for further testing and refinement before moving on to mass production.
R&D Phase | Product Development Phase |
---|---|
Extensive research and development | Testing under various conditions |
Determining how to integrate technological innovations | Refining software integration |
Fine-tuning existing features | Compatibility testing with third-party apps |
The Manufacturing Process
- Sourcing of Raw Materials: The first step in the manufacturing process is sourcing the necessary raw materials. This includes aluminum for the casing, glass for the display, lithium-ion batteries, circuit boards, and various other components. Apple works with suppliers from around the world to ensure that these materials meet their high standards for quality and sustainability.
- Component Fabrication: Once the raw materials are obtained, they undergo various fabrication processes to create the individual components of the iPad. This includes shaping and molding the aluminum casing, cutting and polishing the glass display, manufacturing the circuit boards, and assembling other internal components such as the camera, speakers, and battery.
- Assembly Line Production: After all components are fabricated, they are brought together on assembly lines where skilled technicians meticulously assemble each part to create a fully functional iPad. Specialized machinery assists in this process to ensure precision and efficiency.
- Quality Control Checks: Throughout the entire manufacturing process, rigorous quality control checks are performed to guarantee that each iPad meets Apple’s strict standards for reliability and performance. This includes thorough testing of every function and feature of the device before it moves on to packaging.
- Final Assembly and Testing: Once all internal components are assembled into the casing of the iPad, final testing is conducted to ensure that everything is functioning as intended. Software is installed, cameras are calibrated, batteries are charged – every aspect of the device is meticulously inspected before it gets packaged for distribution.
Understanding how an iPad is made gives consumers a deeper appreciation for the amount of engineering, technology, and labor that goes into creating these devices. From sourcing raw materials to final assembly and testing, each step in the manufacturing process plays a crucial role in producing a high-quality product that has become an integral part of our daily lives.
Quality Control and Testing
Once the components of an iPad have been assembled, it undergoes rigorous quality control and testing to ensure that every unit meets the highest standards set by Apple. This process is crucial in guaranteeing the reliability and performance of every iPad that reaches the hands of consumers.
The quality control and testing phase includes several important steps to ensure that the iPad functions as intended. These steps may include:
- Visual inspection: Each iPad is visually inspected for any physical defects such as scratches, dents, or discoloration.
- Functionality testing: The functionality of each component, including the screen, camera, connectivity features, and internal hardware, is thoroughly tested to ensure optimal performance.
- Performance testing: iPads are subjected to various tests to evaluate their speed, battery life, and overall performance under different usage scenarios.
In addition to these standard tests, iPads also undergo extensive durability and reliability testing. This may include drop tests to assess impact resistance, environmental testing to evaluate performance in extreme temperatures and humidity levels, as well as extensive battery life testing. All these tests are conducted to ensure that each iPad can withstand real-world usage conditions and deliver exceptional reliability for its users.
Overall, the quality control and testing phase plays a crucial role in upholding Apple’s commitment to delivering high-quality products. It ensures that every iPad that leaves the manufacturing facility meets the stringent standards set by Apple for reliability and performance, providing consumers with a product they can trust for years to come.
The Role of Automation and Human Labor in iPad Production
The production of iPads involves a delicate balance between automation and human labor. This process begins with the gathering and processing of raw materials, such as aluminum, glass, and plastic, which are used to create the various components of the device. These materials are often shaped and assembled using automated machinery, which helps to streamline the manufacturing process and ensure precision and efficiency.
One key aspect of automation in iPad production is the use of robotics for tasks such as welding, assembly, and quality control. Robotics play a crucial role in ensuring that each iPad is assembled with accuracy and consistency, while also reducing the risk of errors or defects in the final product. This level of automation not only helps to speed up production but also enhances the overall quality of each device.
Despite the significant role of automation in iPad production, human labor remains essential at various stages of the manufacturing process. Skilled workers are needed to oversee the operation of automated machinery, perform intricate assembly tasks that require a level of dexterity beyond what machines can currently achieve, and conduct thorough quality control inspections to identify any imperfections or issues that may arise during production.
In essence, the production of iPads relies on a harmonious blend of automation and human labor. While automation contributes to efficiency and precision in manufacturing, human workers bring their expertise, critical thinking skills, and attention to detail to ensure that each iPad meets the high standards set by Apple. This combination ultimately results in a product that reflects both technological innovation and skilled craftsmanship.
Automation | Human Labor |
---|---|
Streamlines manufacturing process | Provides expertise and critical thinking skills |
Ensures precision and efficiency | Performs intricate assembly tasks |
Conducts thorough quality control inspections | Oversees operation of automated machinery |
Environmental Impact
The environmental impact of electronic devices, including iPads, has become an increasingly important concern as technology continues to advance. In this section, we will explore the sustainability practices involved in the manufacturing of iPads and the steps taken to minimize their environmental footprint.
Use of Recycled Materials
One of the key sustainability practices in iPad manufacturing is the use of recycled materials. Apple has committed to using recycled aluminum in the enclosure of their products, including iPads. This not only reduces the demand for newly mined aluminum but also lessens the energy required for production.
Energy Efficiency and Renewable Energy
Another crucial aspect of sustainability in iPad manufacturing is energy efficiency and the use of renewable energy sources. Apple has made significant strides in reducing energy consumption at its manufacturing facilities, as well as transitioning to renewable energy sources such as solar power. This helps lower greenhouse gas emissions and lessen the environmental impact of producing iPads.
Waste Management and Recycling Programs
Proper waste management and recycling programs are integral to sustainable manufacturing practices. Apple has implemented comprehensive recycling programs to responsibly manage e-waste from iPads and other devices. This includes initiatives aimed at extending product lifespan through refurbishment and recycling materials at the end of a device’s life cycle.
These sustainability practices demonstrate that while electronic devices like iPads are undeniably intricate and valuable in today’s society, efforts are being made to ensure their production aligns with environmental stewardship and responsibility. By prioritizing the use of recycled materials, adopting energy-efficient processes, and implementing waste management initiatives, Apple is working towards reducing the environmental impact of iPad manufacturing.
The Final Product
After exploring the intricate process of how an iPad is made, it’s important to consider the final stages of its journey. Once the iPad has been manufactured and tested for quality control, it goes through packaging and distribution before reaching consumers.
The packaging of the iPad is carefully designed to not only protect the device during transportation but also to create a memorable unboxing experience for the customer. This attention to detail is just one of the many ways in which Apple ensures that every aspect of their product reflects their commitment to excellence.
Once packaged, iPads are distributed worldwide through a complex network of logistics and supply chain management. From shipping by air or sea to international customs clearance and local distribution centers, there are countless steps involved in getting iPads into the hands of eager customers around the globe. Furthermore, Apple employs targeted marketing strategies to create buzz around new iPad releases, utilizing a combination of social media, advertising campaigns, and retail promotions.
In conclusion, the journey of an iPad from concept to reality is a truly remarkable process that involves cutting-edge technology, skilled labor, stringent quality control measures, and a commitment to sustainability. As consumers eagerly anticipate each new release from Apple, they can now appreciate the extensive efforts that go into making each iPad a technological marvel worthy of its reputation.
Understanding how an iPad is made allows us to further appreciate the craftsmanship involved in bringing such a sophisticated device to market.